Fasteners and Machining: Tailored Solutions for each Production Demand
Fasteners and Machining: Tailored Solutions for each Production Demand
Blog Article
Navigating the Globe of Fasteners and Machining: Techniques for Accuracy and Speed
In the complex realm of bolts and machining, the mission for precision and rate is a continuous difficulty that requires meticulous focus to detail and critical planning. From comprehending the varied selection of fastener types to selecting ideal products that can hold up against strenuous needs, each action in the process plays a pivotal duty in achieving the desired outcome. Precision machining techniques additionally boost the complexity of this craft, requiring a delicate equilibrium in between technological experience and ingenious strategies. As we explore the techniques that can improve both speed and performance in this domain name, the interplay between quality assurance procedures and functional quality arises as an essential centerpiece.
Understanding Fastener Types
When selecting fasteners for a job, understanding the numerous kinds offered is vital for making sure ideal performance and reliability. Bolts come in a large range of types, each developed for specific applications and demands. Screws are made use of with nuts to hold products with each other, while screws are functional bolts that can be used with or without a nut, depending on the application. Nuts, on the various other hand, are internally threaded bolts that mate with screws or bolts, supplying a protected hold. Washers are essential for dispersing the tons of the fastener and avoiding damages to the material being attached. Additionally, rivets are permanent bolts that are suitable for applications where disassembly is not required. Recognizing the differences in between these bolt types is vital for choosing the right one for the task, making sure that the link is strong, resilient, and reliable. By choosing the suitable bolt type, you can maximize the performance and durability of your task - Fasteners and Machining.
Selecting the Right Products
Comprehending the relevance of selecting the best products is extremely important in ensuring the optimal performance and dependability of the picked bolt types talked about previously. When it pertains to fasteners and machining applications, the material choice plays a critical duty in identifying the general stamina, longevity, rust resistance, and compatibility with the intended atmosphere. Various products offer differing residential properties that can considerably influence the efficiency of the bolts.
Usual products used for bolts consist of steel, stainless-steel, titanium, light weight aluminum, and brass, each having its unique staminas and weaknesses. Steel is renowned for its high toughness and longevity, making it ideal for a variety of applications. Stainless steel provides exceptional corrosion resistance, ideal for environments vulnerable to moisture and chemicals. Light weight aluminum is lightweight and corrosion-resistant, making it appropriate for applications where weight decrease is important. Brass is typically chosen for its visual allure and exceptional conductivity. Titanium is known for its exceptional strength-to-weight proportion, making it perfect for high-performance applications. Selecting the appropriate material involves taking into consideration factors such as toughness demands, environmental conditions, and spending plan restrictions to guarantee the wanted performance and longevity of the bolts.
Accuracy Machining Techniques
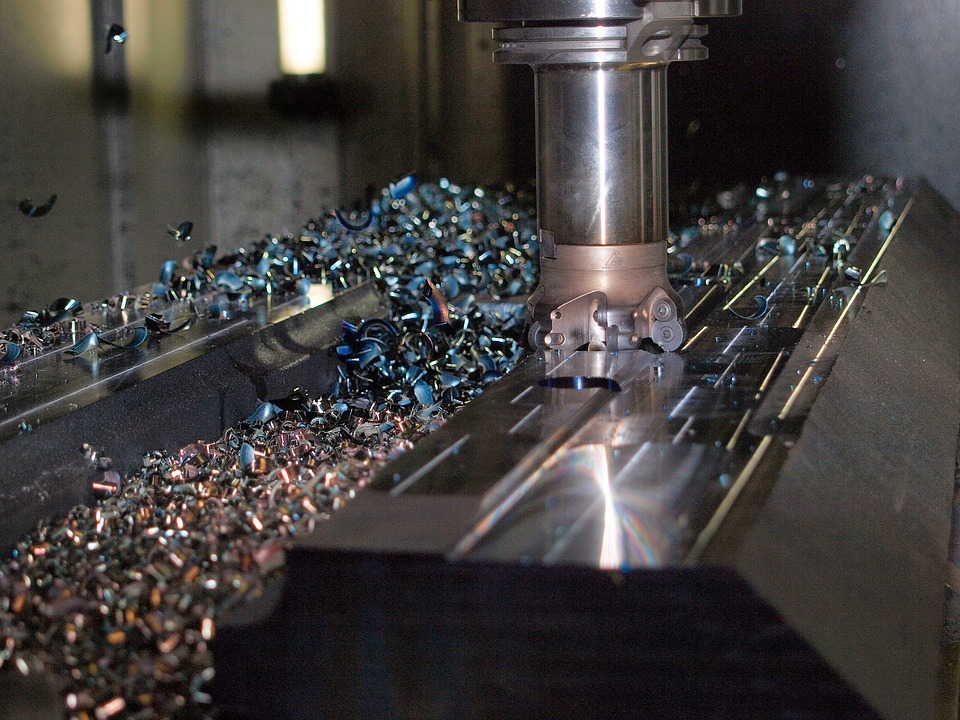
Along with CNC machining, various other precision techniques like grinding, transforming, milling, and drilling play vital duties in bolt production. Grinding assists accomplish great surface finishes and tight dimensional resistances, while transforming is often used to develop cylindrical parts with precise sizes. Milling and boring procedures are essential for forming and producing holes in bolts, guaranteeing they fulfill precise specifications and feature appropriately.
Enhancing Rate and Performance
To maximize fastener production processes, it is crucial to streamline operations and apply effective strategies that complement accuracy machining strategies. One essential technique for boosting rate and performance is the execution of lean production concepts. By reducing waste and concentrating on continuous renovation, lean techniques help optimize and remove bottlenecks process. In addition, buying automation modern technologies can dramatically enhance production speed. Automated systems can deal with repeated jobs with accuracy and speed, allowing workers to concentrate on even more facility and value-added tasks. Embracing Just-In-Time (JIT) stock administration can likewise boost performance by ensuring that the appropriate products are offered at the correct time, lessening excess stock and decreasing lead times. Fostering a society of partnership and communication amongst group members can enhance total effectiveness by promoting openness, problem-solving, and innovation. By incorporating these strategies, producers can attain an equilibrium between rate and precision, inevitably improving their one-upmanship in the bolt sector.
Quality Assurance Measures
Applying extensive high quality control measures is crucial in guaranteeing the dependability and consistency of bolt products in find more information the production procedure. Fasteners and Machining. Quality control steps encompass different stages, beginning from the choice of raw materials to the last evaluation of the ended up fasteners. This involves examining elements such as product structure, resilience, and toughness to assure that the fasteners fulfill market criteria.
Normal calibration of devices and equipment is check my reference important to keep consistency in production and make certain that fasteners satisfy the needed tolerances. Carrying out rigorous protocols for recognizing and addressing non-conformities or issues is vital in stopping substandard items from entering the marketplace. By establishing an extensive top quality control structure, manufacturers can maintain the online reputation of their brand and deliver fasteners that satisfy the greatest criteria of efficiency and resilience.
Final Thought
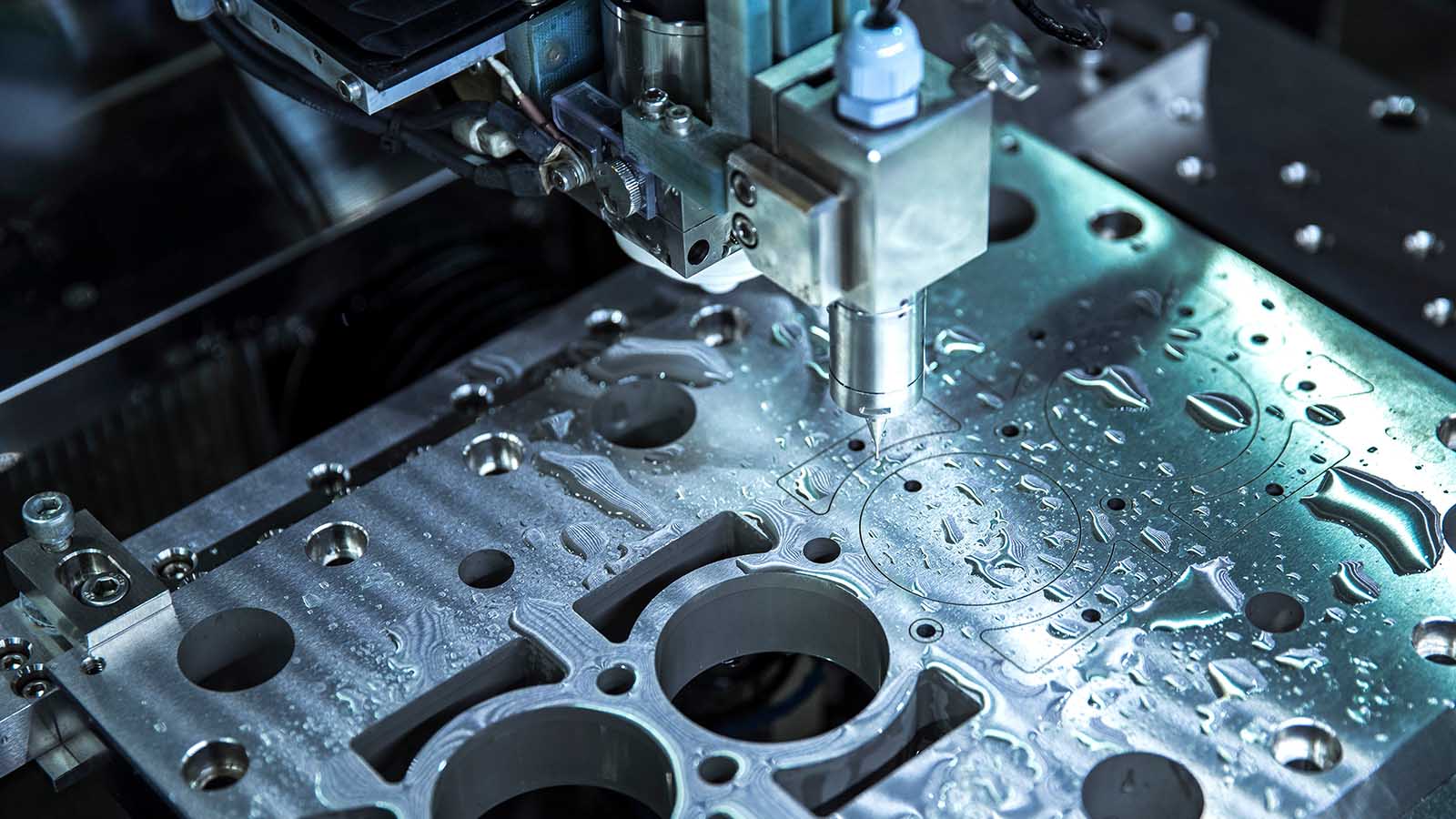
In the intricate realm of bolts and machining, the pursuit for accuracy and speed is a continuous check this site out obstacle that requires thorough attention to detail and calculated preparation. When it comes to bolts and machining applications, the material selection plays an essential function in figuring out the general stamina, toughness, rust resistance, and compatibility with the designated atmosphere. Precision machining involves numerous innovative techniques that make sure the tight tolerances and requirements required for fasteners.In enhancement to CNC machining, other accuracy strategies like grinding, transforming, milling, and drilling play essential functions in fastener production.To optimize bolt production processes, it is crucial to streamline procedures and apply reliable methods that match precision machining strategies.
Report this page